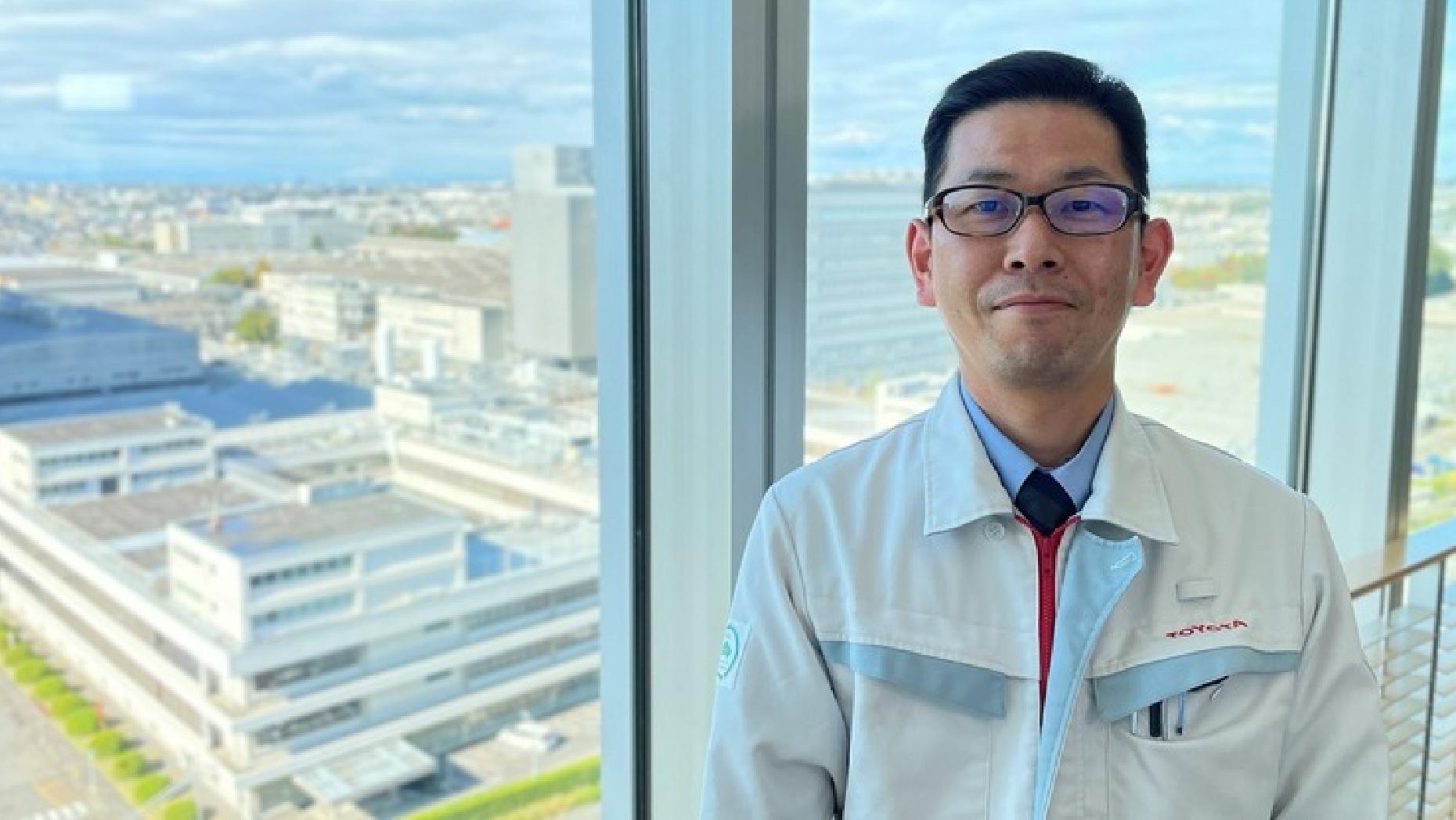
現場に足を運んで汗をかき、
泥臭く製品企画に挑む
モビリティ技術・デジタルソフト開発
MSZ
K.N
現場に足を運んで汗をかき、
泥臭く製品企画に挑む
モビリティ技術・デジタルソフト開発
MSZ
K.N
ミッドサイズビークルカンパニーで製品企画を担当するK.N。2023年現在はクラウンの車両立上げ業務と初期品質向上活動のリーダーを務めています。入社以来16年間設計に従事し、全社横断プロジェクトの指揮を執った経験を活かし魅力的なクルマづくりを牽引するK.Nが、仕事の醍醐味や自身の信念について語ります。
車両の立上げと
品質向上活動に従事。
ミッションは、
魅力的なクルマをつくること
2022年1月からミッドサイズビークル(以下、MS)カンパニーのMSボデー設計部からMS製品企画(以下、Z)に異動し、クラウンシリーズを担当しています。現在は車両ラインオフ(出荷)に向け、工場に常駐し立上げを推進するRE(Resident Engineering)活動と、出荷後、販売店様やお客様にお渡しする中でいただくご意見を受け、製品をさらに磨き上げ、クラウンおよび後続車にフィードバックする初期品質向上活動のリーダーをしています。
このZは「アルファベットの最後=車両の最終責任を負う」と言われています。
Zの業務は車両企画に始まり、開発の推進、量産・発売準備、立上げ後の改善など車両のライフサイクルすべてに関わります。それぞれのフェーズで、Zとして進むべき道を示し、関係する仲間を巻き込みながら、魅力的な車両を作り上げていくことがミッションです。私の場合は、量産準備フェーズでこの役割を果たすことが求められていました。
トヨタ自動車では、クルマを骨格から見直し、基本性能と商品力を大幅に向上させるクルマづくりの構造改革、“TNGA(Toyota New Global Architecture)”に取り組み、生産効率と開発効率のさらなる向上のために、素のいい部品を賢く共用化して開発を進めています。
そんな中、印象的な出来事がありました。あるとき、他車種で異音が発生したと連絡が入りました。クラウンでも同じ部品を搭載しています。立上げ直前の段階でしたから影響台数は180台。ラインオフは目前です。対応するには完成車をリフトアップし対策品に交換、さらに再検査が必要など時間と人と手間がともないます。発生確率は非常に低いという情報もありました。正直に言うと対応すべきか悩んだのも事実です。でも、ここはやはり現地現物。異音を再現したクラウンを作り、実際に走って異音を体感し、「これではお客様にお届けできない」と腹を括りました。お客様には目の前の1台がすべてです。できることはすべてやろうと工場に協力をお願いして、部品を交換する方向へ舵を切りました。
工場からは「大変だが対策しよう。まず対象台数を把握したい。半日で」と檄が飛びます。180台すべてを交換すると出荷延期にもなる規模です。お客様を待たせないという強い意思があり、その準備をするためにも半日で台数把握が必要でした。選別方法を見つけるために設計担当とクルマの下に潜り込み、どこを見れば選別できるか確認。工場や各部には人員確保をお願いしつつ、待つ間に工場メンバーと効率的な選別作業を計画しました。夕方には関係者が集まり作業確認の後、作業に取り掛かりました。そこからはみんなで背中をドロドロにしながら、異音を起こす条件に該当する車両を一斉に選別しました。
工場側のリクエスト通り台数把握を行うことができ、出荷までの限られた時間の中で、何とか部品交換を実現する計画を立案することができ、結果的に遅延なく出荷できました。仕入先様を始め、多くの仲間の協力があったからこそ実現できたと思います。
車両の責任を持つという重み、納期を守る重み、その両方を学んだ出来事でした。量産準備フェーズでは期限が迫っているためギリギリの判断が続きます。それでも甘い判断をせず進めることができたのは、工場にどっぷりと浸からせてもらい、共に汗を流す仲間ができ、リアルな車両がある環境で、現場に足を運んで、現物を見て触って判断をできたからだと思います。この泥臭い仕事のスタイルは今後も忘れず徹底していきたいと思います。
全社の
防錆プロジェクトを率いて、
全車両の品質向上を実現
大学時代は工学部で航空宇宙工学を学びました。就職先に航空業界ではなく自動車業界に進んだのは潜在的にクルマに特別な愛着を感じていたからだと思います。子どものころ、父は年に1度はクルマで海水浴に連れて行ってくれました。このときの思い出は今でも鮮明で、家族とクルマと共に過ごした原風景として残っています。クルマは普段から町中で見かける身近な存在。そんな製品づくりに携わる仕事がしたいと思い、トヨタを志望しました。
入社してから2021年までの16年間、ずっと設計の仕事をしてきました。トヨタにはさまざまな企画業務がありますが、設計の中にも企画業務は存在します。その中でも印象的だったのは、2016年から2018年にかけてMSボデー設計部で担当した、防錆(金属部品の錆びを防止する表面処理や塗装処理)品質の向上をミッションとした全車の品質向上計画の立案です。
最初に見たのは防錆評価後の車両でした。欧州メーカーとトヨタの車両が並んでおり、同じ評価をしたにも関わらず、その差の大きさにショックを受けました。なんとしても防錆品質を向上しなければという想いで取り組みを始めました。
まず、社内に危機感を醸成するために、競合車をベンチマークして、時代ごとの防錆の仕様変化を視える化し、トヨタの立ち位置について知ってもらうよう努めました。
次に対策の選択です。防錆アイテムはいろいろあり、それらを車両のどこに、どのように使えば性能向上に寄与するか確認しながら決めていきます。新規で開発した材料もありました。
そして、塗装時期。防錆に重要な塗装工程は、世界各国の工場ごとにレイアウトに差もあれば、生産中の車両があり、すぐに工事はできないなど、個別の配慮が必要になります。そこで、国内も海外も出張時にはその地域の工場の塗装工程を必ず見学し、足元の事情を把握しました。こうすればできる──開発日程を睨み、このタイミングならできる──。これらを繰り返して、全工場かつ全車両の矛盾のないレベルアップ計画を立案しました。
最後は原価低減です。品質と原価を天秤にかけてはいけませんが、品質を向上すれば多くの場合、原価は上がる傾向にあります。品質第一は揺るぎませんが、原価も大事な要素です。グローバルで見れば錆の厳しい地域、緩い地域が存在します。そこで地域ごとに仕様の適正化を図ったり、材料を輸出ではなく現地で手配できるようにしたり、世界レベルで見たときにコストアップになっていない計画を作りあげました。そして、ようやく防錆品質向上計画が承認され、実行に移すことができました。
欧州に錆調査に行った際、現地販売店で働く仲間と夕飯に行ったのですが、「赤錆を想起させるから、赤ワインはダメ」と言われたのです。冗談混じりの発言でしたが、言いようのない悔しさを覚え、「10年後には赤ワインを飲めるようにします」と約束しました。あれから6年ほど経過し、防錆プロジェクトのミッションの達成が現実味を帯びてきました。お客様の声を直接聞き、考動した結果、世の期待にも応えられていると確信しています。
各現場で汗を流す
たくさんの人の想いを
つなぎあわせ、
かたちあるものに
設計畑一筋で歩んできましたが、入社17年目に製品企画へ異動しました。これまではプラットフォームの設計がメインで車種を跨ぐ仕事だったので、クラウンという個車を中心に仕事を進めていくことはとても新鮮です。
これまで、ある部品のみの責任を負っていたところから、クルマを構成する約3万点もの部品の責任を一手に背負う立場になりました。知識が追いつかない部品もまだまだありますし、ソフトの制御などは自分には未知の分野です。車両になることで営業や広報との関わりも増えています。質問を受けたり問題が起きたりするたびに、必死で勉強し、知識を増やすことから一歩ずつ始めています。毎日が新しいことの出会いで、幸せなことだと思っています。
慣れない仕事に挑戦する中で、モチベーションの源泉となっているのは、最終的にお客様の声が聞けること。そして、開発段階でさまざまな人が汗を流しながら頑張っている姿を目にすると刺激を受けます。いろいろな人の想いをつないで理想をかたちにしていく過程そのものにも大きなやりがいを感じています。
また、「企画は山の上から眺めるだけでなく、山を下りて汗を流すことも大事」と肝に銘じながら仕事に打ち込んでいます。クラウンがお客様の手元に届き、私たちの考えが及ばなかったことでご迷惑をおかけすることがあります。サービスの仲間が現場に行き、謝り、不具合の原因を突き止め、修理してお返しする。自分が行かなくても解決はできます。
しかし、同行することを大事にしています。現場で生の声を聴き、仲間の苦労している姿を見て、同じ場で汗を流し、次同じことをしないためにどうすべきかを考える。この経験を繰り返すことが、企画を担う者がふたたび山に登り、全体を俯瞰して進むべき道を決めるときに必ず役に立つと考えています。こうした姿勢が取れる風土が社内の全体に根付いています。先輩方から長く受け継がれてきた、トヨタゆえの強みだと感じます。
専門領域を備えた
プロフェッショナル揃いの
チームで任務を遂行
クラウンは16代目を迎えるにあたり、社長から「原点に戻り、これからのクラウンを本気で考えよう」との言葉から開発がスタートしています。このときはMSカンパニーの中で、チーフエンジニアと各機能リーダーが集まる組織ができ、「クラウンとは何か」「もっといいクラウン」のためにと、企画と開発が一体となって即断即決で開発が推進されました。
開発が落ち着き、量産体制に入るタイミングからはチーフエンジニアのもと、新たなメンバーを中心にプロジェクトを進めています。それぞれバックグラウンドや得意領域は異なります。エンジン適合/Zの経験者がクラウンの車両全体をマネジメント、内装設計出身者が発売準備の取りまとめを、ボデー設計出身の私が生産準備と出荷後の品質向上の責任を担い、シャシー/Zの経験者が次の年次改良に向けた企画に携わっています。コアな領域を持ちながら、協力して車両全体をマネジメントする多能工な職場と言えると思います。
また、クラウンは群戦略で開発していますので後続車種を担当しているメンバーもいます。およその責任範囲は明確ですが、専門知識が必要なときはサポートに入るなど、群の中で柔軟に対応しています。ミッションの実現に向けてそれぞれが愚直に取り組みながら、毎日のミーティングの場で互いの仕事、進捗を確認し合い、個人商店化しないよう進めています。
ひとつの車種を量産させることに責任を持って取り組み、世の中に向けてリリースした後にお客様からフィードバックをいただき、それをさらなる改善につなげてクルマの完成度を高めていく、駅伝で言うと製品企画の最後の10区を走らせてもらったと思います。9区まで走ったメンバーの汗や想い、襷をつなげてくれた結果があってのことです。製品企画は広く、そして奥が深く、自分で走っていない他の区の走り方を学ぶのはこれからです。10区を走った経験を活かして他の区を現地現物で走ってみたいですね。
世の中の変化、開発の変化もあり、きっと厳しいとは思いますが、自分らしい旗を立てて、お客様のために製品企画の山登りをしていきたいと思います。その先に、モビリティを通したお客様の幸せが待っていると信じています。
未来のクルマを創造するための先端研究や先行開発、そこで生まれた技術を製品に仕立てる製品開発を担当しています。自分たちが新しい未来を想像して描く。常に新しいものを考えて生み出す難しさと魅力がここにはあります。
入社形態:
職種:
本部・コース:
形式:
キーワード:
FindInterview
あなたが読みたい社員インタビューを
選択してください。